Solar cell and method of manufacture thereof, and solar cell module
a solar cell and module technology, applied in the field of solar cells, can solve the problems of increasing the resistance of the collecting electrode, the increase of the internal resistance of the solar cell, and the high material cost of silver, so as to improve the conversion efficiency of the solar cell and achieve the effect of low resistance, high efficiency and low cos
- Summary
- Abstract
- Description
- Claims
- Application Information
AI Technical Summary
Benefits of technology
Problems solved by technology
Method used
Examples
example 1
[0136]A heterojunction solar cell of Example 1 was manufactured in the following manner.
[0137]An n-type single-crystal silicon wafer having a light incident surface direction identical to the (100) surface and having a thickness of 200 μm was provided as a single-crystal silicon substrate of a first conductivity type. The silicon wafer was immersed in a 2 wt % aqueous HF solution for 3 minutes to remove silicon oxide covering on the surface, and thereafter rinsed twice with ultrapure water. The silicon substrate was immersed in a 5 / 15 wt % aqueous KOH / isopropyl alcohol solution held at 70° C. for 15 minutes, and the surface of the wafer was etched to form a textured surface. Thereafter, the wafer was rinsed twice with ultrapure water. The surface of the wafer was observed using an atomic force microscope (AFM manufactured by Pacific Nanotechnology, Inc.), and it was confirmed that the surface of the wafer was mostly etched, and a pyramidal texture surface exposed at the (111) plane ...
examples 2 to 4
[0147]A heterojunction solar cell was prepared in the same manner as in Example 1 except that the ratio of a metallic material powder to a silver powder in the printing paste for forming the first electroconductive layer 71 was changed as shown in Table 1.
examples 5 and 6
[0148]A heterojunction solar cell was prepared in the same manner as in Example 1 except that the thickness of the insulating layer 9 was changed as shown in Table 1.
PUM
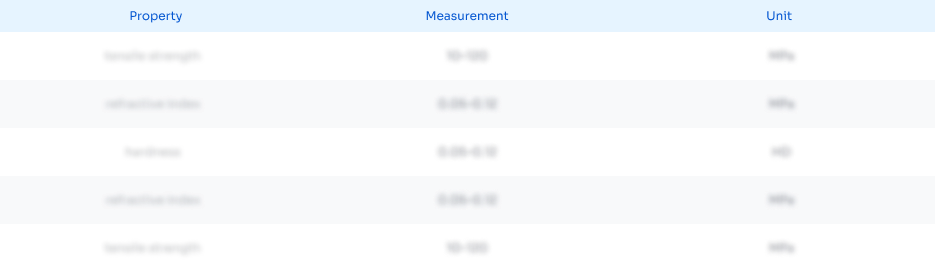
Abstract
Description
Claims
Application Information
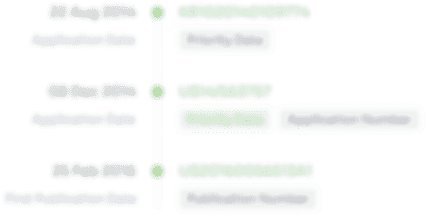
- R&D Engineer
- R&D Manager
- IP Professional
- Industry Leading Data Capabilities
- Powerful AI technology
- Patent DNA Extraction
Browse by: Latest US Patents, China's latest patents, Technical Efficacy Thesaurus, Application Domain, Technology Topic.
© 2024 PatSnap. All rights reserved.Legal|Privacy policy|Modern Slavery Act Transparency Statement|Sitemap